Professional Guidance on What is Porosity in Welding and Just How to Address It
Wiki Article
Recognizing Porosity in Welding: Checking Out Reasons, Effects, and Prevention Strategies
Porosity in welding is a consistent difficulty that can substantially influence the quality and stability of welds. As professionals in the welding market are cognizant, recognizing the causes, impacts, and prevention strategies connected to porosity is crucial for attaining robust and reliable welds. By delving right into the origin of porosity, analyzing its detrimental effects on weld top quality, and checking out reliable prevention methods, welders can improve their expertise and abilities to produce top quality welds continually. The complex interplay of variables contributing to porosity requires an extensive understanding and an aggressive method to make sure successful welding results.Usual Sources Of Porosity
Porosity in welding is mainly brought on by a mix of aspects such as contamination, improper protecting, and poor gas coverage throughout the welding procedure. Contamination, in the type of dirt, oil, or corrosion on the welding surface, creates gas pockets when heated up, resulting in porosity in the weld. Improper protecting takes place when the protecting gas, commonly utilized in processes like MIG and TIG welding, is unable to completely safeguard the liquified weld swimming pool from responding with the surrounding air, causing gas entrapment and subsequent porosity. Additionally, insufficient gas insurance coverage, commonly as a result of wrong circulation rates or nozzle positioning, can leave components of the weld unprotected, allowing porosity to develop. These elements collectively add to the formation of voids within the weld, compromising its integrity and potentially causing architectural concerns. Recognizing and resolving these typical reasons are crucial steps in protecting against porosity and making certain the quality and strength of welded joints.Results on Weld High Quality
The existence of porosity in a weld can dramatically endanger the total quality and honesty of the welded joint. Porosity within a weld produces voids or tooth cavities that weaken the structure, making it much more prone to breaking, corrosion, and mechanical failing.Moreover, porosity can impede the performance of non-destructive screening (NDT) methods, making it testing to find other issues or gaps within the weld. This can lead to significant safety and security problems, specifically in essential applications where the architectural honesty of the welded elements is paramount.
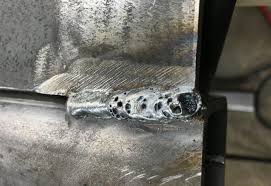
Avoidance Techniques Introduction
Given the detrimental impact of porosity on weld high quality, efficient avoidance techniques are crucial to keeping the architectural honesty of bonded joints. In addition, choosing the ideal welding parameters, such as voltage, present, and take a trip rate, can assist reduce the threat of porosity development. By incorporating these prevention methods right into welding techniques, the incident of porosity can be substantially decreased, leading to more powerful and much more trusted bonded joints.Value of Appropriate Protecting
Appropriate securing in welding plays a vital function in avoiding climatic contamination and ensuring the stability of bonded joints. Protecting gases, such as argon, helium, or a combination of both, are frequently utilized to safeguard the weld swimming check out this site pool from responding with elements airborne like oxygen and nitrogen. When these reactive elements enter call with the hot click for more weld swimming pool, they can create porosity, leading to weak welds with decreased mechanical homes.
Poor securing can lead to different problems like porosity, spatter, and oxidation, endangering the architectural integrity of the bonded joint. Adhering to proper shielding techniques is essential to generate premium welds with very little flaws and make sure the durability and dependability of the welded elements.
Surveillance and Control Methods
Exactly how can welders effectively keep an Go Here eye on and regulate the welding procedure to guarantee optimum outcomes and protect against flaws like porosity? One secret method is via the use of advanced monitoring innovations. These can consist of real-time tracking systems that offer responses on parameters such as voltage, current, take a trip speed, and gas flow prices. By constantly keeping track of these variables, welders can identify inconsistencies from the optimal problems and make instant changes to stop porosity development.
In addition, implementing appropriate training programs for welders is crucial for keeping an eye on and controlling the welding procedure efficiently. What is Porosity. Informing welders on the significance of keeping consistent criteria, such as proper gas shielding and travel rate, can aid avoid porosity concerns. Routine assessments and qualifications can likewise make sure that welders are competent in tracking and regulating welding processes
Moreover, the use of automated welding systems can enhance surveillance and control capabilities. These systems can specifically control welding parameters, minimizing the possibility of human mistake and guaranteeing regular weld high quality. By integrating innovative tracking innovations, training programs, and automated systems, welders can efficiently keep track of and control the welding process to decrease porosity issues and attain high-grade welds.
Verdict

Report this wiki page